Renault passe de l’industrie 4.0 au métavers industriel
Tout connecter et tout assembler : Renault l’a fait. Ses jumeaux numériques sont devenus un métavers industriel avec des résultats concrets. Avec 800 millions d’euros d’investissements sur six ans, les économies sont à la fois financières et en impacts environnementaux.

Quand on dit « métavers », on ne peut s’empêcher de songer à des individus se promenant sous forme d’avatars dans une ville virtuelle. Chez Renault, le mot « métavers » renvoie plutôt à une étape de la digitalisation industrielle au-delà de l’usine 4.0. Les avatars ne sont généralement pas humains : il s’agit plutôt de véhicules ou de machines outils. Un « métavers industriel », selon la définition du constructeur automobile, associe les jumeaux numériques de toute la chaîne de production et de la logistique associée, les données en temps réel sur tout ce qui peut se passer dans l’usine ou en lien avec elle (chez les partenaires par exemple) et, enfin, une rétroaction pour piloter la réalité. Et, comme le sujet ne peut pas être évacué, la création du métavers a aussi été l’occasion de refondre en totalité la cybersécurité du SI industriel dont les technologies dataient souvent de plus de vingt ans.
Dès 2016, Renault a lancé un vaste programme de digitalisation industrielle dont le résultat actuel est le métavers industriel. Jusqu’en 2018, avec 120 millions d’euros d’investissements, Renault a mis en place les infrastructures agiles nécessaires à la suite. Puis, de 2019 à 2021, Renault a multiplié les jumeaux numériques de ses chaînes industrielles en y associant de la réalité augmentée et de l’exploitation intensive de la data, le tout grâce à 270 millions d’euros d’investissements. 2021-2022, avec 390 millions d’euros investis, a été la période où s’est mis en place le métavers industriel : approche « data @scale », cyber-supply-chain, tour de contrôle numérique… 800 millions d’euros investis au total ! Aujourd’hui, Renault capture un milliard de jeux de données par jour !
Tout connecter, tout savoir, tout piloter
Pour que le métavers soit techniquement possible, plusieurs choix majeurs ont été opérés. Tout d’abord, la connexion de toutes les machines a dû reposer sur l’usage d’un langage commun et unique à travers tous les outillages, de tous les constructeurs dans toutes les usines. Chaque machine, chaque objet d’une chaîne de production, possède son avatar, son jumeau numérique, qui bénéficie des données capturées en temps réel sur son modèle physique. Au delà des chaînes de production à l’intérieur des usines, 90 % des camions assurant la logistique avec les partenaires sont aujourd’hui connectés dans le métavers industriel et 700 000 véhicules sont tracés de chaque étape de leur production jusqu’à l’arrivée en concession. Toute la réalité de la production de Renault se retrouve donc en temps réel dans une simulation générale et temps réel qui permet aux différents décideurs, à tous les niveaux, de connaître la situation, de repérer le moindre incident et de réagir de la façon la plus appropriée. Renault revendique des économies sur les process industriels atteignant 20 à 30 %. Par dessus les données collectées, le constructeur automobile a évidemment ajouté de l’intelligence artificielle et du machine learning pour accompagner les décideurs humains.
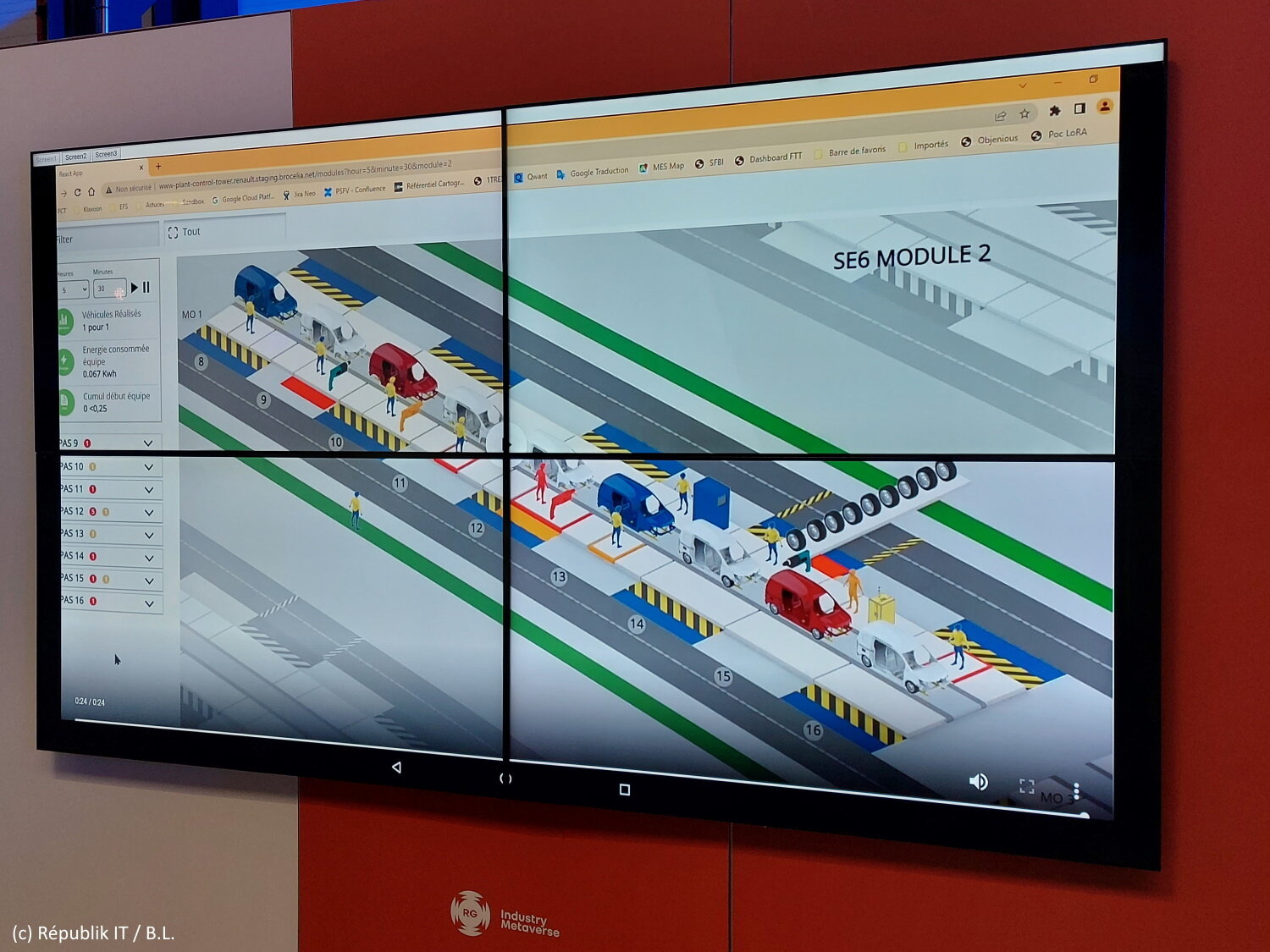
La « tour de contrôle industrielle » permet ainsi de visualiser en temps réel tout ce qui se passe sur une ligne de production. Si elle permet de suivre les objets (machines, véhicules en fabrication…), les opérateurs humains, eux, ne sont vus que comme des postes. Ce ne sont pas les individus qui sont suivis mais une ressource de production : si un opérateur connaît un problème ou s’il s’absente, il apparaît en rouge sur le métavers de l’usine et le responsable adéquat peut alors réagir. Chaque position de travail est également dotée de tablettes qui accompagnent le travail de chaque opérateur sur l’ensemble de son service. Il peut également utiliser cette tablette pour valider ce qui se passe, remonter des alertes, clôturer un incident…
Des choix techniques forts
Côté infrastructures, Renault s’appuie sur un partenaire autant transnational que lui : Google. Celui-ci lui fournit un « cloud edge ». De quoi s’agit-il ? L’apparent oxymore désigne en fait le recours à un cloud public et à une extension locale, sur les mêmes technologies. En effet, pour des questions de réactivité et de fiabilité, les usines ne peuvent pas trop compter sur des données stockées au loin. Ce qui est immédiatement nécessaire est donc stocké localement (en mode edge), le reste étant dans le cloud public traditionnel. Au fil de la fabrication, les jumeaux numériques de chaque objet sont enrichis, mis à jour, puis, lorsque l’immédiateté n’est plus requise, archivés dans le cloud public pour garder une traçabilité totale, y compris pour l’analyse d’optimisation. A l’horizon 2025, Renault attend un gain de 320 millions d’euros par an sur la production, de 260 millions sur les stocks, une baisse de 50 % sur le coût environnemental en CO² par véhicule fabriqué, une réduction du délai de livraison d’un véhicule commandé de 60 %…
En effet, si le métavers industriel est avant tout du traitement de données en temps réel, les données sont bien conservées et retraitées « à froid » pour optimiser les processus après-coup. Au delà de la production proprement dite, connecter 10 000 compteurs de ressources (eau, gaz, électricité…) a permis de créer un suivi des consommations dans le métavers, prendre des décisions de production selon la météo ou les tarifs du moment (éviter une forte consommation électrique lorsqu’il y a pic général de consommation par exemple), réduire les consommations quand cela est possible et… négocier avec les fournisseurs. Que ce soit en temps réel ou en différé, il existe cependant une règle intangible : si l’IA propose ou alerte, c’est bien l’humain qui décide. Mais l’IA peut apporter une vraie plus-value à l’être humain. Par exemple, la start-up Buawei a fourni sa solution PokAIok pour contrôler en temps réel la qualité industrielle. Une caméra visualise les pièces, éventuellement sous un angle difficile pour un être humain, lit le cas échéant des références sur une étiquette et repère les anomalies : mauvaise référence, déformation, etc. Et Renault diffuse ensuite chaque innovation, chaque modèle d’analyse, dans toutes les usines où c’est pertinent à travers le monde puisque toutes fonctionnent sur les mêmes bases. Le constructeur est si satisfait de son « Industrial Data Platform », le socle de son métavers industriel, qu’il a confié à Atos la commercialisation de celui-ci auprès d’autres industriels.
Former les opérateurs grâce à la réalité virtuelle
Les opérateurs doivent bien sûr être formés à leurs postes. Cela passe par des exercices pratiques ou de la vidéo mais aussi par de la réalité virtuelle immersive. Dans l’exemple en photo ci-contre, l’opérateur peut s’entraîner virtuellement à peindre un véhicule en optimisant ses gestes. Il s’agit d’éviter que des zones soient insuffisamment ou au contraire trop peintes. Au delà de l’économie de peinture et de la meilleure qualité du produit fini, il y a aussi un enjeu environnemental évident. A la fin d’un exercice, la réalité virtuelle montre à l’opérateur le résultat de son travail, colorant les zones selon que la peinture a été trop, pas assez ou correctement abondante.
L’impression 3D, source de nouveaux business models
Renault utilise, comme beaucoup d’autres industriels, l’impression 3D additive pour ses prototypes. Mais le constructeur automobile permet aussi de concevoir et de fabriquer des outils pour améliorer la performance. Une fois un outil mis au point pour faciliter une opération industrielle, son schéma est diffusé mondialement pour profiter à toutes les usines. Parfois, certaines pièces de véhicule manquantes ou complémentaires peuvent être produites en impression 3D additive. Mais ces pièces complémentaires peuvent aussi être originales et à l’origine de personnalisations. L’impression 3D n’est pas adaptée à de grosses séries de production mais dégage tous ses bénéfices dans, précisément, la petite série. Il est ainsi envisagé de permettre à des clients de demander des options de personnalisation. Dans la photographie ci-contre, les pièces en rouge sont de telles personnalisations, des objets demandés par certains types de clients comme des artisans par exemple. Chez Alpine, qui produit uniquement en petites séries, ce sont des personnalisations décoratives qui sont réalisées en impression 3D.
Sur le même sujet
Pour un métavers pluriel, varié et interopérable
Les Agences de Papa vont lancer la vente immobilière via univers virtuel